試験と検査 - 錠剤とカプセル
テストと検査
試験と検査 - 錠剤とカプセル
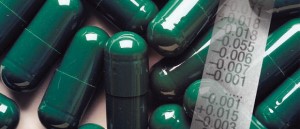
試験と検査 - 錠剤とカプセル
品質を組み込むことでカプセルの目視検査を削減します。
テストと検査
錠剤とカプセルから
処方製造包装
第6巻第1号
2008年1月
品質管理を徹底することでカプセルの目視検査を削減
ジム・ムーアヘッド バイオキャップス エンタープライズ
この記事では、目視によるカプセル検査の限界について説明し、カプセル充填プロセスに品質を組み込む方法について基本的なガイダンスを提供します。
カプセル充填に携わって 37 年になる私は、機械の設置、カプセルの製造、充填、印刷、バンド付けを行ってきました。これらの各ステップで、高品質の製品を確保するために目視検査に頼ることが多かったのですが、もっと良い方法があります。
目視検査の限界
目視検査だけに頼るのは間違いです。面倒で労働集約的であるだけでなく、高品質の完成品が保証されることはほとんどありません。誰もいつまでも集中することはできませんし、ローラー テーブルの上を移動するカプセルを検査する訓練を受けた技術者でさえ、一部の不良品を見逃すことがあります。私はかつて、顧客の施設でテストを実施し、充填済みカプセル 100,000 個のうち 1 バッチに追加した 100 個の不良カプセルを見つけて取り除くよう、最も優秀な検査員に依頼しました。ローラー テーブルを使用して、検査員は 1 回目のパスで 100 個の不良カプセルのうち 60 個を検出して取り除き、2 回目のパスでさらに 27 個を検出して取り除きました。その結果、消費者に届くはずだった不良カプセルが 13 個残りました。企業は、私が「ハント アンド ペック法」と呼ぶ、工程内チェックの目視方法に頼りすぎることがよくあります。これは、技術者が工程内製品をすくい上げ、不良カプセルを探す方法ですが、検査するカプセルの数や、工程と機械の能力をどれだけよく理解しているかは考慮されないこともあります。ほとんどの場合、このような無計画な工程内チェックや目視検査を減らすと、コスト、労力、無駄が削減されます。
検査の改善 ウィリアム・エドワーズ・デミングとジョセフ・ジュランは、現在では統計的工程管理(SPC)と呼ばれているものを確立しました。これは、検査に対して体系的かつ数学的なアプローチを採用するものです [1, 2]。私が勤務した多くの施設では、SPC を使用することで目視検査を大幅に削減することができました。
(SPCはGMP認定ではありませんが、GMP認定プロセスによく適合します。)デミングは、結果を図表やグラフ化することでプロセスが管理されているかどうかを判断するために統計を使用し、管理されていないプロセスを簡単に認識できるようにしました。彼の公式は次のとおりです。
品質 = | 作業の結果 |
総費用 |
品質が高ければ、コストは下がります。コストに重点が置かれると、コストは上がり、品質は下がります。ほとんどのカプセル充填作業は、この公式の正確さを証明しています。たとえば、会社の管理者は、新しいディスクが高価であるという理由で、タンピングタイプのカプセル充填機に適した厚さの投与ディスクの購入を躊躇するかもしれません。ディスクを購入しないことに決めると、短期的には費用を節約できますが、技術者が機械のトラブルシューティングを行う必要があり、管理者が一部の製品をリコールする必要が生じるため、後で会社にさらに費用がかかる可能性があります。
検査プロセスを改善するには、100 個のカプセルを収容できるサンプリング パドル、結果を記録するためのフォーム、およびプロセス容器に簡単にアクセスできるシーフなど、いくつかの安価なサンプリング ツールが必要です。パドルを使用できない場合は、100 個のカプセルを収容できる大きさのカップと小さなプラスチック トレイを使用します。次に、特定の充填装置のサンプリング頻度 (以下で説明) と許容品質限度 (AQL) を決定します。マシンをセットアップし、いくつかのカプセルを処理した後に、正しい重量に達したら、バッチを目視検査します。次に、マシンの能力を示す欠陥の数を決定します。製品が AQL を満たしている場合は、バッチ処理を開始します。指定された間隔でサンプルを採取し、目視検査して、結果を記録します。たとえば、「08:30 にサンプルを採取、割れ、へこみ、接合欠陥なし」などです。プロセスが制御不能になっている場合 (つまり、指定されたカテゴリで不合格品が多すぎる場合)、マシンを停止して問題を特定して修正します。さらに、QC/QA 担当者は 1 ~ 2 時間ごとにコンテナーからサンプルを採取し、SPC が機能しているかどうかを確認する必要があります。

目視検査が必要な場合、ローラー テーブルは、検査員がカプセルのあらゆる部分を検査できる便利なツールです。
提供:メンデル(ニュージャージー州イーストハノーバー)
サンプリング サイズと頻度。理想的なサンプリング サイズと頻度を決定するときは、バッチまたはロット サイズではなく、マシンの機能に注目してください。入荷した材料またはロット終了時の検査値のサンプリング サイズを決定するには、Military Standard 105E を使用できます。ロットの平方根サンプルを採取すると、ロットが AQL を満たしているかどうかがわかりますが、欠陥の潜在的な原因を特定するのに役立ちません。原因は配合またはカプセル充填剤にある可能性があるからです。たとえば、12 セグメントとセグメントあたり 12 穴があり、1 つの穴が破損しているマシンを考えてみましょう。その状況では、ロット サイズの平方根サンプルでは、タイムリーな間隔で採取された継続的なサンプルほど欠陥レベルが適切に示されません。マシンを稼働させる場合、決定要因の 1 つは単位時間あたりの出力 (レート) です。多くの栄養補助食品メーカーはさまざまなメーカーとモデルのカプセル充填機を稼働させているため、充填機の機能と最終的にはレートが異なることに注意してください。もう 1 つの決定要因は、カプセル充填機のセグメント、ブッシング、または充填リングに収まるカプセルの数です。不良品は、配合、カプセル、配置、またはセットアップが原因で発生していますか? 許容できるサンプル サイズとサンプル頻度は、問題が 1 つのセグメント、1 つのブッシング、1 つの穴、またはセットアップ全体にあるかどうかを正確に特定するのに役立ちます。サンプル頻度の目安は、30 分ごとに 100 個のカプセルを検査することです。起動がスムーズに行えば、問題のある配合によってマシンの動作が妨げられたり、カプセルのサプライヤーやカプセルを変更したりしない限り、後で欠陥が発生する可能性は低くなります。
AQL は通常、欠陥を重大、重大、軽微に分類します。これらの分類にはそれぞれ、社内仕様に基づいて「合格」または「不合格」の AQL があります。カプセル充填機で製品欠陥が発生し、修正に機械の調整とかなりのダウンタイムが必要になる場合、製品の製造コストが上昇します。栄養製品が機械の能力を満たしていない場合は、目視による選別が必要になることがあります。
品質管理
ジュランはパレートの法則を作り出した。それによれば、問題の 80 パーセントは通常の原因の 20 パーセントによって引き起こされており、この場合、欠陥のある処方や不適切な設定が原因となっている可能性がある [2, 3]。ジュランによると、品質管理は上層部から始まる。したがって、上層部と中級レベルの管理者は、品質計画、品質管理、品質改善を使用した品質管理のトレーニングを受ける必要がある。品質計画。生産を最適化するために、適切なカプセル、材料、機械部品を購入します。管理者は充填機と全体的なプロセスの仕組みを理解して、機器と互換性のあるコンポーネントを選択する必要があります。また、処方者は製品が実際に機械で実行できるかどうかを判断する必要があります。私はよくスラグ テスターを使用します。これは、フォース ゲージと、投与ディスクの穴と同じ直径のキャビティで構成されています。

目視検査が必要な場合、ローラー テーブルは、検査員がカプセルのあらゆる部分を検査できる便利なツールです。
提供:メンデル(ニュージャージー州イーストハノーバー)
テスターは、ディスクの厚さや、配合がスラグを形成し、ディスクから適切に剥離し、重量制御が良好で機械がクリーンに稼働するかどうかを決定するのに役立ちます。機械の種類によっては、さまざまなテストが必要になる場合があります。品質管理。物理的欠陥や規格外の重量を検出するために工程内チェックを実行し、結果をチャートまたはグラフに記録します。こうすることで、工程が逸脱した場合にすぐに気づいて変更を加えることができます。品質改善。最高のリソースである従業員の意見に耳を傾けてください。従業員は、カプセル充填工程を最高レベルで実行するために必要な配合、部品、修理を理解しています。私はよく「この問題についてマネージャーに伝えたが、無視された」という声を聞きます。一方、同じマネージャーは、専門家とみなされている外部の技術者や修理担当者の意見にも熱心に耳を傾けます。しかし、私は、工程を毎日実行する従業員も非常に多くの貴重な知識を持っていることを学びました。実際、このトピックに関する私の専門知識は、最前線の技術者と長年一緒に仕事をしてきたことに由来しています。サプライヤーにアドバイスを求めたり、このような出版物でヒントを探したりすることもできます。機器メーカーがタンピング スタイルのマシンにタンピング ピンを取り付けるのには理由があります。使用するためです。私が目にするタンピング スタイルのマシンの 90% は、正しくタンピングされていないか、まったくタンピングされていません。真空テイクオフやその他のデバイスも理由があって取り付けられているので、取り外さないでください。自動マシンが適切にセットアップされ、適切なサイズの投与ディスクが使用され、互換性のあるフォーミュラが実行されると、目視検査と無駄がほとんどなくなります。
インライン検査装置を設置することも、製品の品質を向上させるもう 1 つの方法です。これらの装置は、割れたカプセル、つぶれたカプセル、空のカプセル、およびカプセルの破片を取り除くことができます。ほとんどのカプセル充填機では、通常、配合と充填量が物理的欠陥の主な原因です。機械とカプセルの能力を把握し、これらの能力を満たすように製品を配合すれば、コスト、労力、および無駄を削減できます。デミングの公式に忠実に、製品に品質を投入すれば、顧客に品質を提供できます。
利用規約
参考文献
1. デミング、WE 1986. 危機からの脱出。マサチューセッツ州ケンブリッジ:MIT プレス。
2. Juran, J. 1951. 品質管理ハンドブック。ニューヨーク、ニューヨーク:McGraw-Hill。
3. Juran, J. 1970. 品質計画と分析。ニューヨーク、ニューヨーク:McGraw-Hill。
JimMoorhead は、BioCaps Enterprise (9698 Telstar Avenue, Suite 309, El Monte, CA 91731) の技術サービス ディレクターです。
電話626 545 2862、ファックス626 575 2866。ウェブサイト:
www.biocaps.net。ムーアヘッド氏は、数多くのカプセル製造業者の技術サービス担当者として 23 年の経験を持っています。