Test & Inspection- Tablets&Capsules
test & inspection
Test & Inspection- Tablets&Capsules
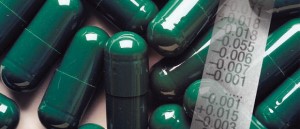
Test & Inspection- Tablets&Capsules
Reduce visual inspection of capsules by building quality in.
Test & Inspection
From TABLETS & CAPSULES
FORMIULATION PRODUCTION PACKAGING
Volume 6 Number 1
January 2008
Reduce visual inspection of capsules by building quality in
JimMoorhead BioCaps Enterprise
This article discusses some limitations of visual capsule inspection and offers basic guidance on how to build quality into your capsule filling process.
Over the course of my 37 years in capsule filling, I have installed machinery and manufactured, filled, printed, and banded capsules. In each of these steps, I often relied on visual inspection to ensure a high-quality product. But there are better ways.
The limitations of visual inspection
Relying solely on visual inspection is a mistake. Not only is it tedious and labor intensive, but it rarely ensures a quality finished product. No one can concentrate indefinitely, and even trained technicians inspecting capsules moving over a roller table will miss some defective products. I once conducted a test at a customer’s facility in which I challenged the best inspector to find and remove the 100 defective capsules I had added to a batch of 100,000 filled capsules. Using a roller table, the inspector detected and removed 60 of the 100 defective capsules in the first pass and another 27 in a second pass. That left 13 defective capsules that could have reached the consumer. Too often, companies rely on a visual method of in-process checking that I call the “hunt-and-peck method.” That’s where technicians scoop through the inprocess product, looking to find defective capsules, sometimes without regard to how many capsules they inspect or how well they understand the process and machine capability. In most cases, if you decrease such haphazard in-process checking—and visual inspection—you’ll reduce costs, labor, and waste.
Improving inspection William Edwards Deming and Joseph Juran established what we now call statistical process control (SPC), which takes a systematic, mathematical approach to inspection [1, 2]. In the many facilities where I’ve worked, using SPC allowed us to greatly reduce visual inspection.
(Although SPC is not GMP certified, it fits well into a GMP-certified process.) Deming used statistics to determine whether a process is in control by charting and graphing the results, which made it easy to recognize an out-of-control process. His formula is
Quality = | Results of work |
Total costs |
When quality is high, costs fall. When costs are the focus, costs rise and quality falls. Most capsule filling operations prove the accuracy of this formula. For example, a company’s managers might balk at buying a dosing disc of the proper thickness for a tamping-type capsule filler because new discs are expensive. Deciding not to buy the disc saves money in the short run, but later it will likely cost the company more because technicians will likely have to troubleshoot the machine and/or managers will have to recall some product.
Improving the inspection process requires a few inexpensive sampling tools: sampling paddles that hold 100 capsules, forms for logging results, and thieves that can reach easily into your process vessels. If you can’t use a paddle, use a cup big enough to hold 100 capsules and a small plastic tray. Next, determine sampling frequency (as discussed below) and acceptable quality limits (AQLs) for your specific filling equipment. Set up the machine, run some capsules, and, after the correct weight is attained, visually inspect the batch. Then determine the number of defects, which informs you about the machine’s capability. If the product meets AQLs, start the batch run. At specified intervals, take a sample, visually inspect it, and record your findings. For example: “Sample taken at 08:30 hours, zero splits, dents, or joining defects.” If the process is out of control (i.e., too many rejects in a specified category), stop the machine and identify and fix the problem. In addition, every 1 to 2 hours your QC/QA personnel should take thief samples from the container to determine whether the SPC is working.

When visual inspection is necessary, a roller table is a helpful tool that allows the inspector to examine every part of the capsule.
Courtesy of Mendel, East Hanover, NJ
Sampling size and frequency.When determining your ideal sampling size and frequency, look at the machine capabilities, not the batch or lot size. To determine the sampling size for incoming material or end-of-lot inspection values, you can use Military Standard 105E. Taking a square root sample of the lot will let you know whether the lot meets your AQLs, but it won’t help you determine the potential cause of defects, since the formula or capsule filler may be to blame. Consider, for example, a machine with 12 segments and 12 holes per segment that has one damaged hole. In that situation, a square root sample of the lot size will not adequately show the defect level that an ongoing sample taken at timely intervals will. When you are running a machine, one determining factor should be the output per unit of time (rate). Since many nutritional supplement manufacturers run capsule fillers of various makes and models, keep in mind that the fillers will have different capabilities and ultimately different rates. Another determining factor is how many capsules fit in the segments, bushings, or filling rings of your capsule filler. Are rejects caused by the formulation, capsules, alignment, or setup? An acceptable sample size and sample frequency can help pinpoint whether the problem is one segment, one bushing, one hole, or the entire setup. A rule of thumb for sample frequency is to inspect 100 capsules every 30 minutes. If startup goes smoothly, it’s likely that there will be few defects later, unless a problematic formula hampers machine operation or you switch capsule suppliers or capsules.
AQLs usually classify defects as critical, major, or minor. Each of these classifications has a “pass” or “reject” AQL based on your in-house specifications. If the capsule filler creates a product defect that requires machine adjustments and sizable downtime to correct, then the cost to produce the product will rise. In some cases where nutritional products don’t meet machine capabilities, some visual sorting will be necessary.
Qualitymanagement
Juran coined the Pareto Principle, which states that 80 percent of problems is caused by 20 percent of the usual causes, which in this case could be a flawed formulation or improper setup [2, 3]. According to Juran, quality management begins at the top. Therefore, top- and middle-level managers should be trained in quality management using quality planning, quality control, and quality improvement. Quality planning. Buy the right capsules, materials, and machine parts to optimize production. Managers should understand how the filling machine and the overall process work so they can select components compatible to their equipment, and formulators should determine whether a product can truly run on the machine. I often use a slug tester, which comprises a force gauge and a cavity with a diameter equal to that of the dosing disc hole.

When visual inspection is necessary, a roller table is a helpful tool that allows the inspector to examine every part of the capsule.
Courtesy of Mendel, East Hanover, NJ
The tester helps determine how thick the disc must be and whether the formulation will form a slug, release from the disc properly, and contribute to a clean-running machine with good weight control. Depending on the style of machine, different tests may be necessary. Quality control. Perform in-process checks to detect physical defects and out-of-spec weight, then record the results in a chart or graph. That way, when a process strays, you can notice it quickly and make changes. Quality improvement. Listen to your best resources— your employees. They understand the formulas, parts, and repairs necessary for the capsule filling process to perform at the highest level. I hear it all the time: “I told my managers about this problem, but they ignored me.” Meanwhile, the same managers eagerly listen to outside technicians and repair people because they are the presumed experts. But I’ve learned that employees who run the process every day possess a great deal of valuable knowledge, too. In fact, my expertise on this topic stems from many years of working with front-line technicians. You can also ask your suppliers for advice and look for tips in publications like this one. There’s a reason that the equipment manufacturers put tamping pins on your tamping-style machine—to be used! Ninety percent of the tamping style machines I see are either tamping incorrectly or not tamping at all. Vacuum take-offs and other devices are also installed for a reason, so don’t disconnect them. When your automatic machine is set up properly, uses a properly sized dosing disc, and runs a compatible formula, you will eliminate most visual inspection and waste.
Installing in-line inspection equipment is another way to improve product quality. These devices can remove split, mashed, and empty capsules and capsule fragments. On most capsule filling machines, the formulation and fill volume are usually the primary causes of physical defects. If you know the machine and capsule capabilities and formulate your product to meet these capabilities, you will reduce costs, labor, and waste. True to Deming’s formula, when you put quality into the product, you will deliver quality to the customer.
T&C
References
1. Deming, W.E. 1986. Out of the Crisis. Cambridge, MA: MIT Press.
2. Juran, J. 1951. Quality Control Handbook. New York, New York: McGraw-Hill.
3. Juran, J. 1970. Quality Planning and Analysis. New York, New York: McGraw-Hill.
JimMoorhead is director of technical service at BioCaps Enterprise, 9698 Telstar Avenue, Suite 309, El Monte, CA 91731.
Tel. 626 545 2862, fax 626 575 2866. Website:
www.biocaps.net.Moorhead has 23 years’ experience as a technical service representative for a number of capsule manufacturers.